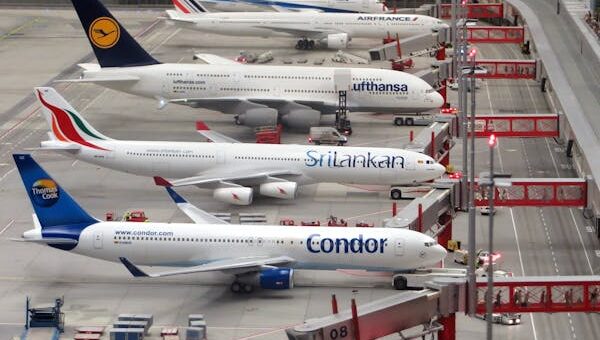
Introduction
Commercial aircraft are among the most complex and costly machines in the world. Airlines invest billions in their fleets, making the lifespan of these planes a critical factor in operational efficiency, financial planning, and safety. But what exactly is the average lifespan of a commercial aircraft? This question involves numerous variables, from aircraft design and maintenance to usage patterns and regulatory requirements. In this detailed article, we will explore the concept of aircraft lifespan, factors that influence durability, maintenance and refurbishment strategies, and how evolving technology impacts the operational lives of commercial planes.
1. Defining the Lifespan of a Commercial Aircraft
1.1 What Constitutes Aircraft Lifespan?
The lifespan of a commercial aircraft can be defined in several ways. It often refers to the total number of years an aircraft remains in active service with airlines. Alternatively, it can be measured by the number of flight cycles (takeoffs and landings) or total flight hours accumulated before retirement.
-
Calendar Years: Most commercial jets are designed for around 20-30 years of operational use.
-
Flight Cycles: Aircraft like the Boeing 737 or Airbus A320 typically have a certified design lifespan of 20,000 to 60,000 cycles.
-
Flight Hours: Many aircraft are designed for approximately 70,000 to 100,000 flight hours.
Each measurement impacts maintenance schedules and retirement decisions differently, emphasizing that aircraft lifespan is a multifaceted concept.
1.2 Regulatory and Manufacturer Guidelines
Aircraft manufacturers provide guidelines based on rigorous testing and certification processes. Regulatory bodies such as the Federal Aviation Administration (FAA) and European Union Aviation Safety Agency (EASA) impose strict maintenance and inspection standards throughout an aircraft’s operational life. These rules ensure continued airworthiness but also indirectly influence how long an aircraft remains in service.
2. Key Factors Influencing Aircraft Lifespan
2.1 Design and Build Quality
The fundamental design and manufacturing quality heavily influence aircraft longevity. Modern commercial aircraft are engineered to endure high stresses and environmental factors such as corrosion, temperature fluctuations, and mechanical fatigue.
-
Use of corrosion-resistant materials.
-
Advanced structural design to distribute stress.
-
Incorporation of redundant systems to enhance safety and durability.
Older models may have shorter lifespans due to less advanced engineering or materials, while newer planes benefit from continuous improvements.
2.2 Operational Usage
How an aircraft is operated greatly affects its wear and tear. Variables include:
-
Flight Length: Short-haul flights tend to increase the number of takeoff and landing cycles, which exert more stress on the aircraft structure.
-
Frequency of Flights: High utilization rates accelerate maintenance needs.
-
Environmental Conditions: Exposure to harsh climates (saltwater, extreme cold) can cause faster corrosion or fatigue.
For example, a plane flying frequent short routes may reach its cycle limit before its flight hours are fully used, influencing retirement timing.
2.3 Maintenance and Overhaul Practices
Regular and thorough maintenance extends aircraft life significantly. Airlines follow detailed maintenance programs mandated by manufacturers and regulators, including:
-
Scheduled inspections (A, B, C, and D checks).
-
Component replacements and upgrades.
-
Structural repairs and corrosion control.
A well-maintained aircraft can operate safely well beyond its original design life, sometimes exceeding 30 years in service.
3. Maintenance Programs and Their Impact on Lifespan
3.1 Overview of Aircraft Maintenance Checks
Aircraft maintenance is divided into several levels, each progressively more detailed and time-consuming:
-
A-Check: Light inspections every 400-600 flight hours.
-
B-Check: More thorough, every 6-8 months.
-
C-Check: Comprehensive checks every 20-24 months, requiring significant downtime.
-
D-Check: The most extensive overhaul, every 6-10 years, involving complete disassembly and inspection.
These checks ensure the aircraft remains safe and airworthy, identifying issues before they become critical.
3.2 Role of Predictive Maintenance
Modern airlines increasingly use predictive maintenance tools powered by data analytics and sensors. These technologies forecast potential component failures before they occur, reducing unscheduled downtime and allowing more efficient life extension.
-
Condition monitoring systems.
-
Engine health tracking.
-
Structural fatigue analysis.
Such advances help maximize aircraft availability while maintaining safety.
4. Economic and Operational Considerations in Aircraft Retirement
4.1 Cost of Maintaining Older Aircraft
As aircraft age, maintenance costs rise due to increasing wear, obsolescence of parts, and labor-intensive inspections. Airlines must balance maintenance expenses against operational efficiency and fuel consumption. Older models may consume more fuel and require more frequent repairs, making them less economical.
4.2 Market Value and Fleet Modernization
Depreciation reduces the market value of older aircraft. Many airlines retire or sell older planes as they invest in newer, more fuel-efficient models that lower operational costs and emissions.
-
New generation aircraft offer improved performance.
-
Modern avionics and systems enhance reliability.
-
Compliance with stricter environmental standards.
Table: Comparison of Operating Costs: New vs. Older Aircraft
Parameter | New Aircraft (e.g., Boeing 787) | Older Aircraft (e.g., Boeing 767) |
---|---|---|
Fuel Efficiency | ~20-30% better | Lower |
Maintenance Costs | Lower | Higher |
Emissions | Reduced | Higher |
Market Value | Higher | Lower |
5. Trends and Innovations Affecting Aircraft Lifespan
5.1 Advances in Materials and Design
New materials like carbon fiber composites are lighter and more resistant to corrosion, enabling longer service lives and improved fuel efficiency.
5.2 Regulatory Changes and Sustainability Goals
Stricter environmental regulations push airlines to retire older aircraft sooner or retrofit them with greener technologies. Sustainability initiatives encourage fleet renewal cycles.
5.3 Aircraft Life Extension Programs
Some airlines and manufacturers offer life extension programs that include structural reinforcements, avionics upgrades, and engine overhauls, allowing older aircraft to continue operating safely and efficiently.
Conclusion
The average lifespan of a commercial aircraft is influenced by a complex interplay of design, usage, maintenance, and economic factors. While many aircraft operate safely for 20 to 30 years or more, advances in technology and stricter environmental regulations are shaping the future of aircraft longevity. How do you see the balance between maintaining older aircraft and investing in new models evolving? Share your thoughts and experiences with aircraft lifespan and fleet management to continue this engaging discussion.